Injection Molding Magnets
Did you know?
Amazing Magnets produces high-quality injection molded parts with unique over molding capabilities.
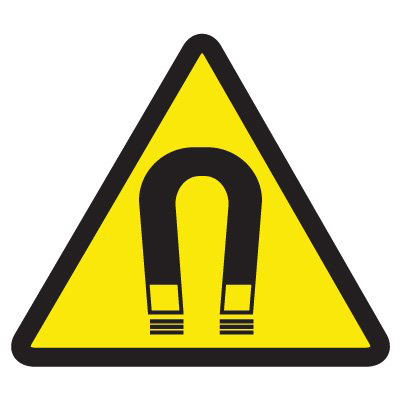
Safety:
Loose or dislodged magnets can be dangerous in consumer products, it is important to safely secure the magnets, so they will never pop out.
Talk to one of our experienced design engineers for assistance in selecting the ideal solution for your product.
Phone: 512-678-2940

Demagnetization:
Magnets will become demagnetized by the high-heat of injection molding. High temperature magnets are available but are more expensive and too brittle for many applications.
Amazing Magnets offers a unique post-mold magnetization process that allows our neodymium magnets to be over molded before magnetization.
The finished parts are then taken to one of our specialized magnetization machines to be fully charged.
Magnet Integration Options:
Insert Molding
Over Molding
Ultrasonic Welding
Other Methods
Insert Molding
Insert molding is a process where the unmagnetized “magnet” is held inside the mold during the injection. This allows the molten plastic to flow around the magnet and lock it into place.
Once the molding is complete and the magnetic material is cooled, the entire product can be placed into one of our special magnetization machines to be charged and fully magnetized.
Holding the magnet in place during injection:
Molten plastic is injected at high pressure.
The magnet must be held securely during this process to prevent it from moving during the injection phase.
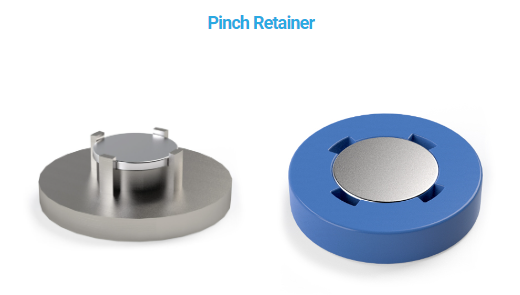
The magnet can be held by a series of pins on the mold that surround it, pinching it in place during the injection process.
When the part is demolded from the plastic, these pins leave holes in the plastic.
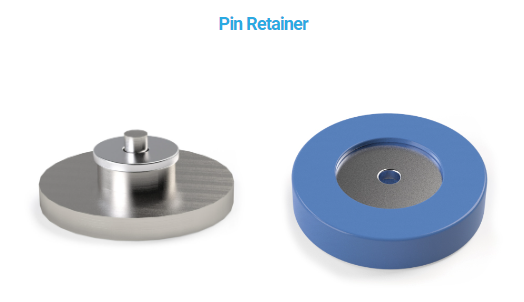
A pin on the mold is inserted to a matching hole in the magnet. Pin holes are usually 2 – 6 mm in diameter, depending on the magnet size.
When the part is demolded, the pin is removed, leaving a hole in the magnet.
Holding the magnet after injection:
After insert molding the magnet should be retained by the plastic. This could be a feature in the magnet such as a groove or step, or in the plastic component that surrounds the magnet. Below are a few commonly used methods for retaining the magnet via insert molding.
Plastic Cover
The magnet may be partially covered by plastic on both sides to hold it in place.
This feature may be combined with a pinch retainer or pin retainer to hold the magnet during injection.
Grooved Magnet
A groove is created in the magnet to hold it in place.
This feature may be combined with a pin retainer to hold the magnet during injection.
Stepped Magnet
A step feature is created on the magnet to hold it in place. This feature may be combined with a pinch retainer or pin retainer to hold the magnet during injection.
Insert Molded Steel Backer
A steel disc is molded inside the plastic. A fully charged magnet can then be attached to the molded steel disc afterwards in a separate assembly process.
Other Magnet Integration Options
Over-Molding
Over-Molding or a “2-shot mold” offers the ability to create fully encapsulated magnets. This is a common requirement when the magnet will be exposed to harsh environments, or in medical applications.
This process involves 2 separate molds. The first mold creates a plastic part with a cavity for the magnet. The magnet is then inserted into the first plastic part. The assembly is then placed into the 2nd mold where the 2nd half of the plastic is injected, covering the magnet and fusing with the first half of the plastic.
Ultrasonic Welding
Ultrasonic welding is another way to create fully encapsulated magnets. the part is created as 2 separate pieces. The pieces are then assembled with the magnets and fused together by localized high-frequency vibration.
Snap On
The 2 halves of the plastic component snap together to retain the magnet.
Screw/Bolt
A countersink, or counterbore feature is created in the magnet. The magnet can then be screwed down. Notches and other asymmetric features can be created in round magnets to prevent unwanted rotation.
Melt Rivet
A plastic stud can be melted down into a countersunk cavity in the magnet.
Interested in Custom Magnets or Plastic Components?
We do everything from design, engineering, and prototyping, to full scale production and premium retail packaging.
If you have questions please reach out to customercare@amazingmagnets.com, or you can submit a Request for Quote (RFQ) Online.